December 2024
The manufacturing industry is experiencing a breakthrough started with a machine learning solution – predictive maintenance. This high-tech innovation enables a significant cost reduction in equipment maintenance. For example, the US Department of Energy reports about 70-75% decrease in breakdowns!
What exactly does predictive maintenance stand for?
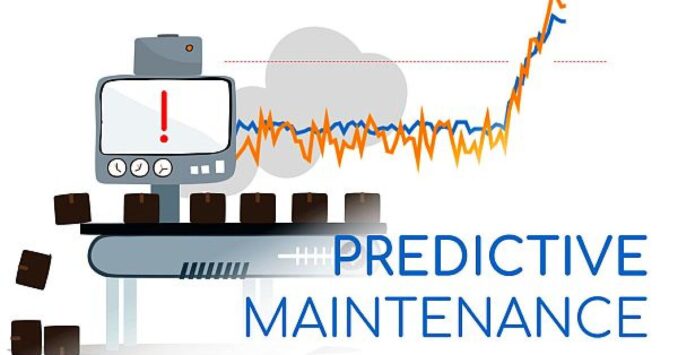
Source:eenewsembedded.com
It’s a strategy that implies monitoring the equipment’s condition, then predicting the possibility of failure and preventing the problem by performing maintenance on time.
Predictive maintenance is a technique based on the fact that most elements of a machine will exhibit some type of “warning” before its failure. Reading these symptoms, which the machine warns us about, requires several types of non-destructive testing.
The application of these techniques to determine the condition of the machine results in significantly more efficient maintenance compared to earlier types of maintenance.
Predictive maintenance allows management to control equipment and maintenance programs. In a company that uses predictive maintenance, the condition of the total equipment is known at all times. This enables significantly more precise planning of downtime and procurement of spare parts, as well as a reduced risk of injuries at work that occur as a result of a crash.
Repairing a machine that failed during operation can be up to ten times more expensive than a planned repair. A large number of new machines fail shortly after commissioning due to failures that occur during the running-in period or due to improper installation. Predictive techniques can be used to ensure proper alignment and overall integrity of the installed machine, during the first commissioning.
So, to state the obvious:
Minimizing the number of occurred failures = saving money on unexpected maintenance
Predictive maintenance has some advantages over scheduled maintenance:
• Increased system reliability
• Reduced maintenance costs
• Reducing the number of maintenance also reduces the impact factor due to human error when performing maintenance
In the same comparison, the disadvantages are:
• High system installation costs, for smaller devices higher than the price of the device
• Due to the maintenance process which is done only when the need arises, they cannot
plan maintenance costs and they are unevenly distributed
• Increased number of components (monitoring system) that require inspection and maintenance
Predictive maintenance systems are not used on less important parts today due to their price visible benefits. A large number of important plants are maintained in this way, which will in the future will be more and more present because the prices of surveillance devices are getting lower every year. Nowadays, predictive maintenance is widely used where it can be carried out without expensive and sophisticated devices.
How does it all work?
There are numerous different approaches when it comes to predictive maintenance techniques.
One of the biggest challenges facing today’s company is its continuing proactivity. The survival of a company in conditions of pronounced competitiveness depends on its ability to think proactively and act. She needs to recognize the opportunities and dangers that lie ahead threatening her, and provide an adequate response. Given that the company’s success in the market very much depends on one’s action, the principle of proactivity should be consistent in its internal business processes, and thus maintenance. Application of new requirements maintenance strategies radical change of organization. This means abandoning the traditional approach maintaining a repair-oriented and reliability-oriented, that is, a shift from reactive to proactive way of thinking.
We need constant change, technological innovation capability, and high productivity to survive in the fiercely competitive environment. – Joe Kaeserl, CEO of Siemens
How to collect data from your equipment?
With the use of data from the Internet of Things sources. Sensors and tools widely used in the IoT industry can connect all the pieces of equipment to a central hub. The connection between a central hub and all the available assets is a basis for predictive maintenance. The collected information can be used by technicians to analyze the condition of the equipment and make a decision if maintenance is required.
However, installing and setting up such a system is a rather complicated task. Implementing predictive maintenance can be quite an investment. Here are some tips on how to limit collected data and minimize costs:
- Focus on crucial pieces of equipment
- Create a reliable database by following questions such as how often the parameters should be measured, and what kind of them, is failure possible and if is, what can you expect, and so on.
- Determine failure modes
Now correlate the selected resources with the collected data. Conduct detailed analysis and identify the failure modes of each piece of equipment you want to “watch”.
- Develop a model
Now is the time to create a predictive maintenance model. While working on it, decide what kind of results you expect from the model. Should it just inform you that something will go wrong or take some steps? Or maybe it depends on each specific failure case? Fill in the details, otherwise, your model will not work properly. When your model is ready, don’t forget to test it.
- Start using your model
If you are satisfied with the test results, deploy the predictive maintenance model, and start using it.
Key benefits of implementing predictive maintenance for your business
To wrap it up, your company will experience:
- Energy savings – predictive maintenance model will keep you updated on the changes in energy consumption which will enable you to introduce more efficient actions and save money.
- Minimize time wasted on equipment maintenance – dedicate your team’s time to activities that will help grow your business.
- Increased competitive advantage – with the services of addepto.com, your investment will pay off quickly, allowing you to focus on new challenges.
The main characteristics of preventive maintenance are the following:
– This is done periodically and routinely.
– It is a type of maintenance whose tasks and budgets are planned. It has a start and end time.
– It is carried out in conditions of complete control to avoid accidents, while the equipment is stopped.
– It seeks to predict future breakdowns or damage to equipment.
– The manufacturer usually recommends when to do this, through technical manuals.
Advertisement
– The activities that are carried out follow the previously prepared program.
– Offers the ability to update the technical configuration of the equipment.
Now you have all the key information you need to improve your business, now go ahead and make a change!